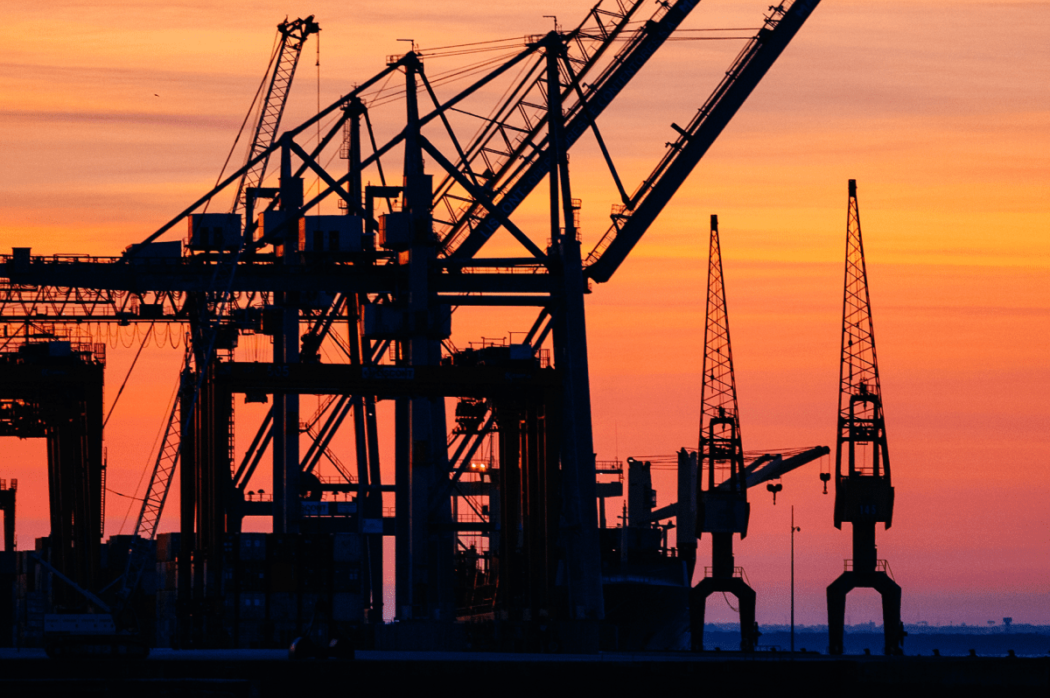
From the casing of your air cooler to the jar of your mixer grinder, injection moulding is the unsung hero of plastic manufacturing. But how does it work — and why is it so critical?
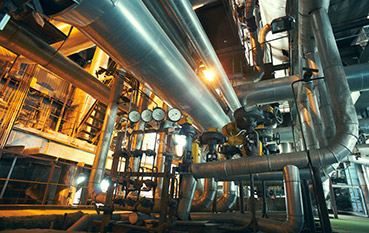
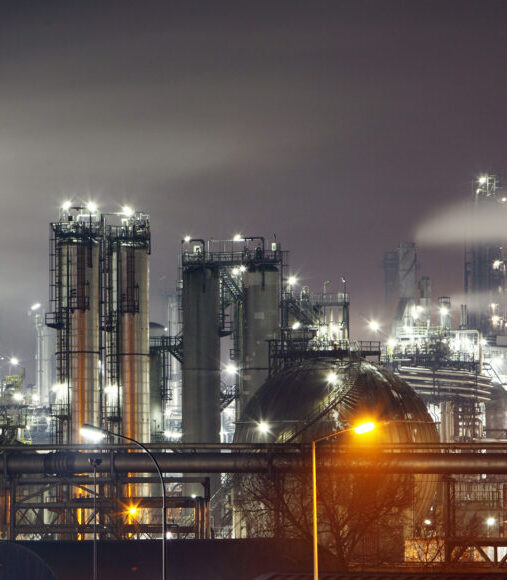
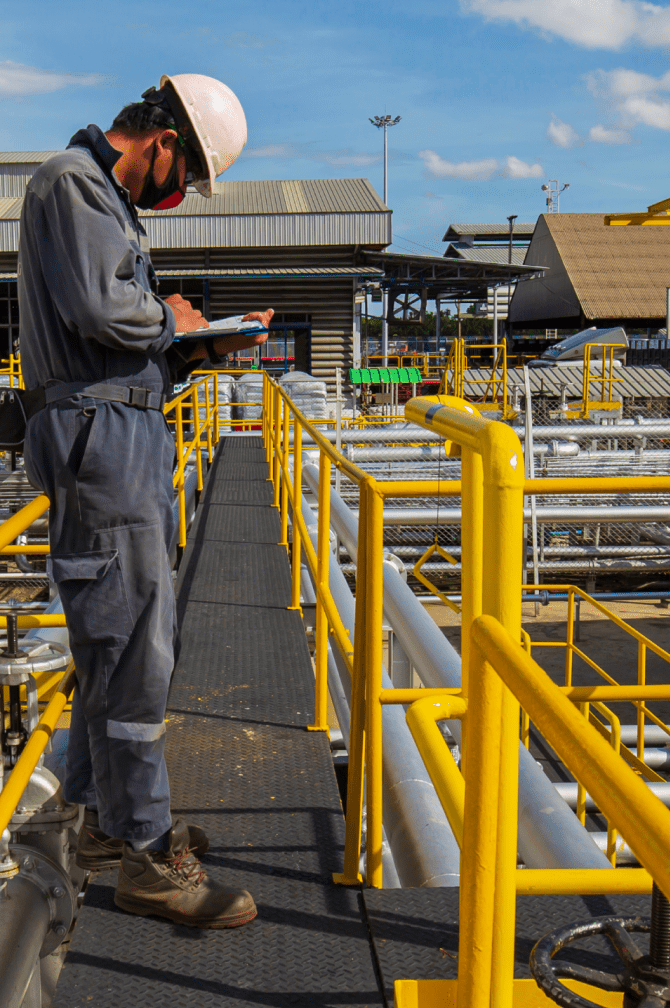
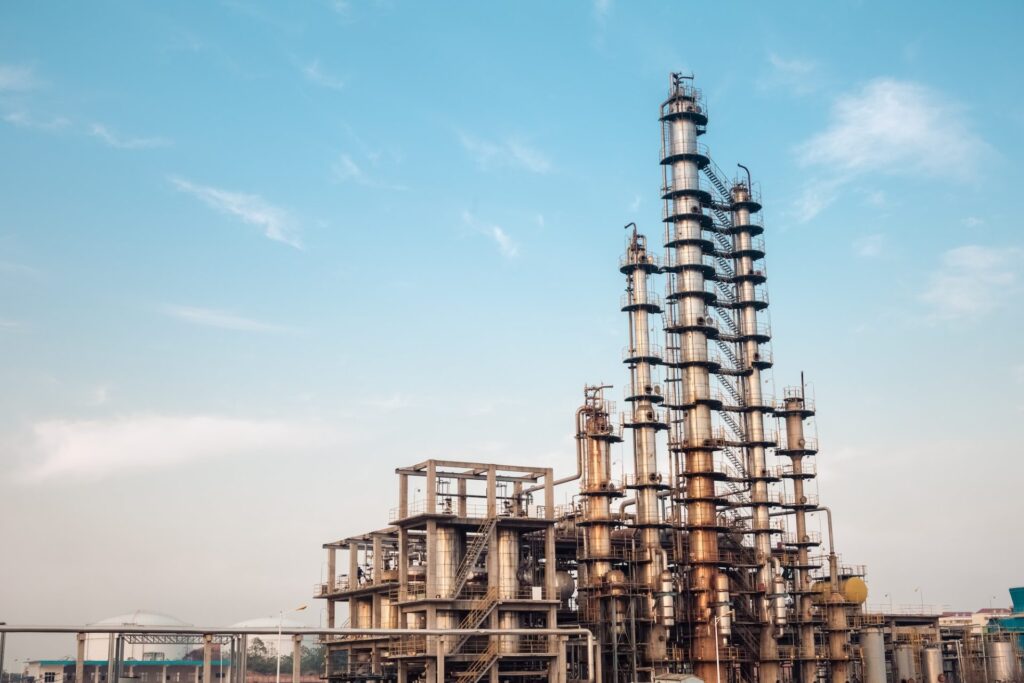
What is Injection Moulding?
Injection moulding is the process of injecting molten plastic into a mould cavity where it cools and hardens into the desired shape. It’s fast, efficient, and perfect for large-volume production.
Our Machinery: Precision at Scale
We use advanced injection moulding machines ranging from 180 to 2100 tons. This range allows us to handle:
- Small detailed components
- Large appliance bodies
- Custom moulds for OEM clients
Benefits of Injection Moulding:
- 🔁 High repeatability
- ⚙️ Complex designs with accuracy
- 📉 Low production waste
- ⏱️ High-speed manufacturing
Our Materials:
We work with a wide range of thermoplastics — chosen based on the application, finish, and durability requirements of each client.
Conclusion:
Injection moulding is at the core of everything we do. And at Compassion Appliances, we’ve mastered the art and science of it — to deliver unmatched quality, speed, and flexibility.